转:APQC PCF – 如何创建端到端流程?(例如,订单到交付)
在知识星球分享了一张 APQC 的构建端到端流程海报的翻译
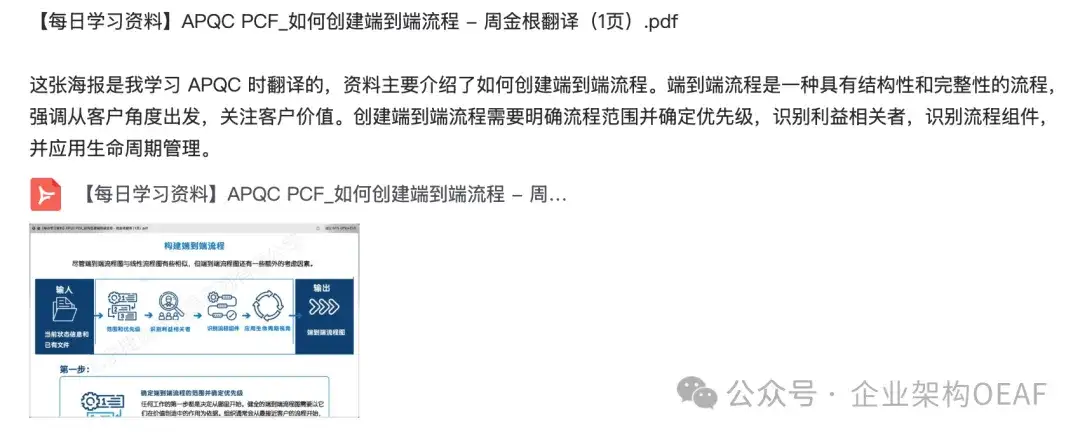
海报主要对端到端流程下了定义,比较了功能性思维与端到端流程思维,最主要是说明了构建端到端流程的四个步骤。
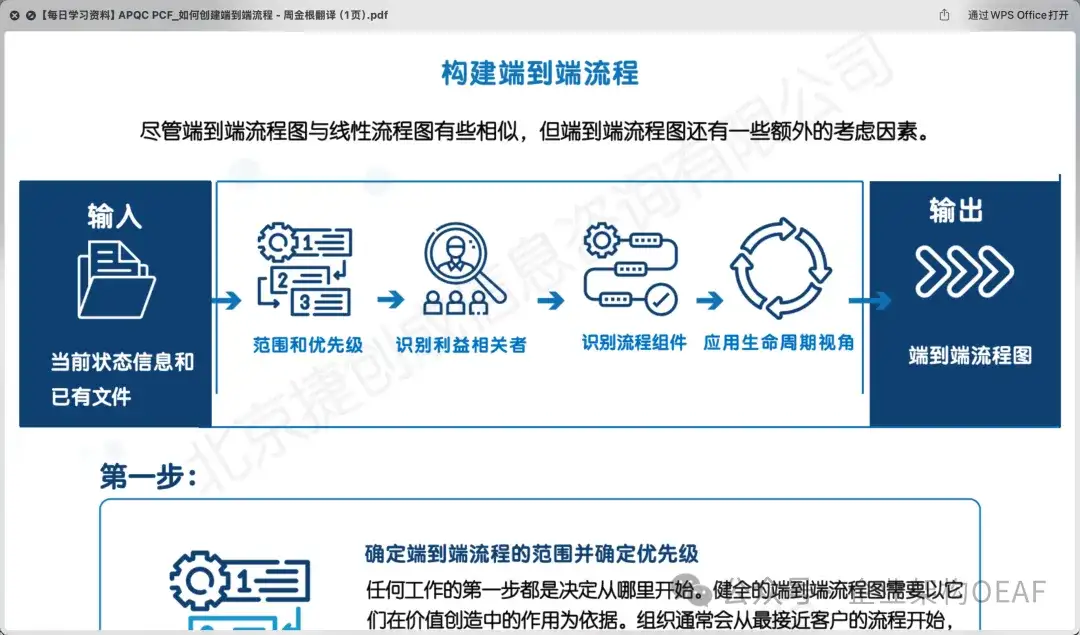
端到端流程也是捷创成内训课程中的一个主要内容,接下来我对这部分内容做下讲解。
端到端(End-to-End, E2E)流程管理是打破部门壁垒、实现业务目标的核心方法。以下是其核心定义、关键标准及构建步骤的详细说明。
一、端到端流程的定义与关键标准
定义: 端到端流程是一个通常具有跨职能性质的完整链条,涵盖实现特定目标所需的所有步骤,从初始触发点到最终交付,确保价值无缝传递。
关键标准:
- 由外向内的视角:从客户或外部需求出发,反向设计流程。
- 涵盖整个价值链:整合从需求识别到价值交付的所有环节,避免局部优化。
- 关注客户价值:确保每个步骤直接或间接贡献于客户体验与价值实现。
- 根据价值对流程进行分类:优先聚焦高价值流程,与组织战略目标对齐。
前面3点大家可能都很容易明白,我分享一下对第4点的理解。总之,“根据价值对流程进行分类”是一种以客户价值为导向的流程管理方法,通过识别和优化高价值流程,提升组织的整体运营效率和客户满意度。我们可以从以下几个方面来理解:
1. 价值导向的分类方式
- 核心思想:将流程按照其为客户创造的价值进行分类,而不是仅仅按照功能部门或任务类型来划分。这意味着流程的分类标准是以客户价值为核心,而不是以组织内部的职能划分。
- 举例:在一个制造企业中,传统的分类方式可能是将流程分为生产流程、物流流程、销售流程等。而基于价值的分类方式则会将流程分为“客户订单到交付”(Order-to-Delivery)流程、“产品设计到上市”(Design-to-Launch)流程等。这些流程都是围绕客户价值展开的,例如“客户订单到交付”流程直接体现了从客户下单到产品交付的全过程,其价值在于满足客户对产品交付速度和质量的需求。
2. 价值驱动的流程管理
- 目的:通过分类,识别和优化那些对客户价值贡献最大的流程,同时减少或优化那些价值贡献较低的流程。
- 举例:在一家电商公司中,“客户购买到售后”流程是高价值流程,因为它直接影响客户的满意度和忠诚度。而一些内部的行政流程(如办公用品采购流程)虽然也是必要的,但其价值相对较低。通过分类,公司可以优先优化“客户购买到售后”流程,以提升客户体验。
3. 价值分类的实施步骤
- 识别价值流:首先需要识别出哪些流程为客户创造了价值,分析每个流程步骤为客户带来的具体价值。
- 分类标准:根据价值流分析的结果,将流程分为高价值流程、中价值流程和低价值流程。例如,高价值流程可能直接与客户接触或直接影响客户满意度;低价值流程可能是内部支持性流程,但仍然需要优化以降低成本。
- 优化与管理:根据分类结果,对高价值流程进行优先优化,确保其高效运行。对于低价值流程,则可以通过精简或自动化等方式降低成本。
二、创建端到端流程的四大步骤
步骤1:确定流程范围并确定优先级
- 核心目标:明确需要优化的端到端流程及其战略优先级。
- 实施方法:
- 以流程在价值创造中的作用为依据,优先选择以下两类流程:
- 最接近客户的流程(如订单处理、客户服务)
- 与竞争优势直接相关且不可分割的流程(如产品创新、供应链管理)
- 通过价值链分析,识别对业务成果影响最大的流程作为起点。
步骤2:识别和吸引利益相关者
- 核心目标:明确所有利益相关者及其需求,确保流程设计满足多方期望。
- 实施方法:
- 列出直接或间接关联的利益相关者(客户、员工、供应商、监管者等)
- 通过调研或访谈,明确:
- 各方的核心诉求与优先级
- 与其互动的最佳方式(如定期沟通、协作工具、反馈机制)
步骤3:识别流程组件
- 核心目标:全面拆解流程的组成部分,建立清晰的当前状态基线。
- 实施方法:
- 数据收集:
- 对主题专家进行深度访谈,获取流程细节
- 组织跨职能研讨会,邀请利益相关者共同梳理流程
- 利用事件日志进行自动化流程挖掘,识别实际执行路径
- 输出成果:
- 详细的流程步骤、决策点、交接节点及责任分配
- 明确瓶颈、冗余或低效环节
步骤4:应用生命周期视角
- 核心目标:从全局视角定义流程范围,确保端到端完整性。
- 实施方法:
- 生命周期范围需涵盖以下要素:
- 可能影响流程的相关环境:如市场变化、法规要求、技术限制
- 关键利益相关者及其需求:确保流程设计符合其核心诉求
- 流程的边界和约束:明确起点、终点、资源限制及合规要求
- 协作团队:由业务流程管理团队、流程编制专家及主题专家共同参与,确保视角全面。
三、成功关键:从理论到实践
- 跨职能协作:通过 RACI 矩阵明确角色分工,避免责任模糊
- 客户价值闭环:在流程各环节嵌入客户反馈机制(如满意度调查)
- 持续改进:定期评估流程绩效,根据数据和利益相关者反馈优化设计
四、案例学习:某电子制造企业的“订单到交付”端到端流程优化
以下通过一个电子制造企业的案例,详细说明如何基于前述四个步骤构建端到端流程,并实现效率与客户价值的提升。
步骤1:确定流程范围并确定优先级
- 背景:该企业面临订单交付周期长、客户投诉率高的问题,管理层决定优先优化“订单到交付”流程。
- 实施过程:
- 价值链分析:该流程直接影响客户满意度(最接近客户),且涉及销售、生产、物流等多个部门(跨职能)。
- 优先级选择:因其与竞争优势(快速交付能力)直接相关,被列为高优先级流程。
步骤2:识别和吸引利益相关者
- 关键利益相关者:
- 客户:关注交货准时率和订单准确性
- 销售团队:需实时跟踪订单状态
- 生产部门:需根据订单需求调整排产计划
- 物流供应商:需确保运输时效与成本平衡
- 质量监管部门:需确保产品符合交付标准
- 互动方式:
- 通过客户满意度调查收集反馈
- 组织跨部门会议,协调销售、生产与物流的协作规则
- 与物流供应商签订SLA(服务水平协议),明确交付时间承诺
步骤3:识别流程组件
- 数据收集方法:
- 主题专家访谈:
- 销售团队:订单接收与确认步骤(如客户需求验证、合同签署)
- 生产部门:生产计划触发条件(如订单优先级规则、物料准备)
- 跨职能研讨会:
- 发现原流程中“订单确认”与“生产排产”之间存在 2 天的信息滞后
- 流程挖掘工具:
- 分析 ERP 系统日志,发现 20% 的订单因物料短缺需人工干预,导致平均延迟 3 天
- 输出成果:
- 流程步骤:订单接收→需求确认→生产排产→物料采购→生产执行→质量检验→物流配送→客户签收。
- 瓶颈环节:物料采购与生产排产的衔接效率低
步骤4:应用生命周期视角
- 生命周期范围定义:
- 外部环境影响:
- 供应链波动(如芯片短缺)可能导致物料延迟
- 客户定制化需求增加,需灵活调整生产计划
- 关键利益相关者需求:
- 客户要求交付周期从 14 缩短至 10 天
- 生产部门需减少紧急插单的频率。
- 流程边界与约束:
- 起点:客户订单提交至系统
- 终点:客户签收并完成付款
- 约束:最大产能限制为每月 5000 台,物流成本需控制在订单金额的 5% 以内。
- 优化措施:
- 引入动态物料预警系统,提前识别短缺风险
- 建立销售与生产的每日同步会议,减少信息滞后
- 在物流环节增加实时追踪功能,客户可通过 APP 查看订单状态
优化成果
- 效率提升:
- 交付周期从 14 天缩短至 9天,准时交付率从 75% 提升至 95%
- 因物料短缺导致的订单延迟减少 60%
- 客户价值提升:
- 客户投诉率下降 40%,NPS(净推荐值)从 30 分升至 65 分
- 成本优化:
- 物流成本占比从 6% 降至 4.5%,年节省约 120万元